SEM-03 in CFD
SEM 03
Our third generation car is a radical change from the cars preceding it. With a switch in competition the entire design needed a rethink. With new rules came new opportunities and limitations. SEM-03 will compete in the prestigious iESC 2026 competition. So far the team has focused on knowing the ruleset inside out and backwards in order to maximise performance and creating initial iterations to express our ideas.
Main Objectives
Main objectives for 24/25:
Design a small, light chassis and wrap low drag low weight carbon fibre bodywork around it to create a light low drag race car.
Procure high quality, powerful motors and batteries to power and store energy for the car.
Develop solar power and electronic power management systems for maximising the energy captured from the sun.
Engineer the SEM team’s first ever suspension system to provide optimum cornering grip at slow speeds.
Main objectives 25/26
Create manufacturing process solutions to plan the manuafcture of all aspects of the car.
Order for manufacture core elements of the car such as the chassis and solar panel array.
Hands-on manuafcture of the boydwork suspenions elements.
Assemble all the parts in a succint and robust manner ready for racing.
Conduct a test day at parkwood karting to test the systems.
Organise logistics for the comeptition including driver choices and strategy plans.
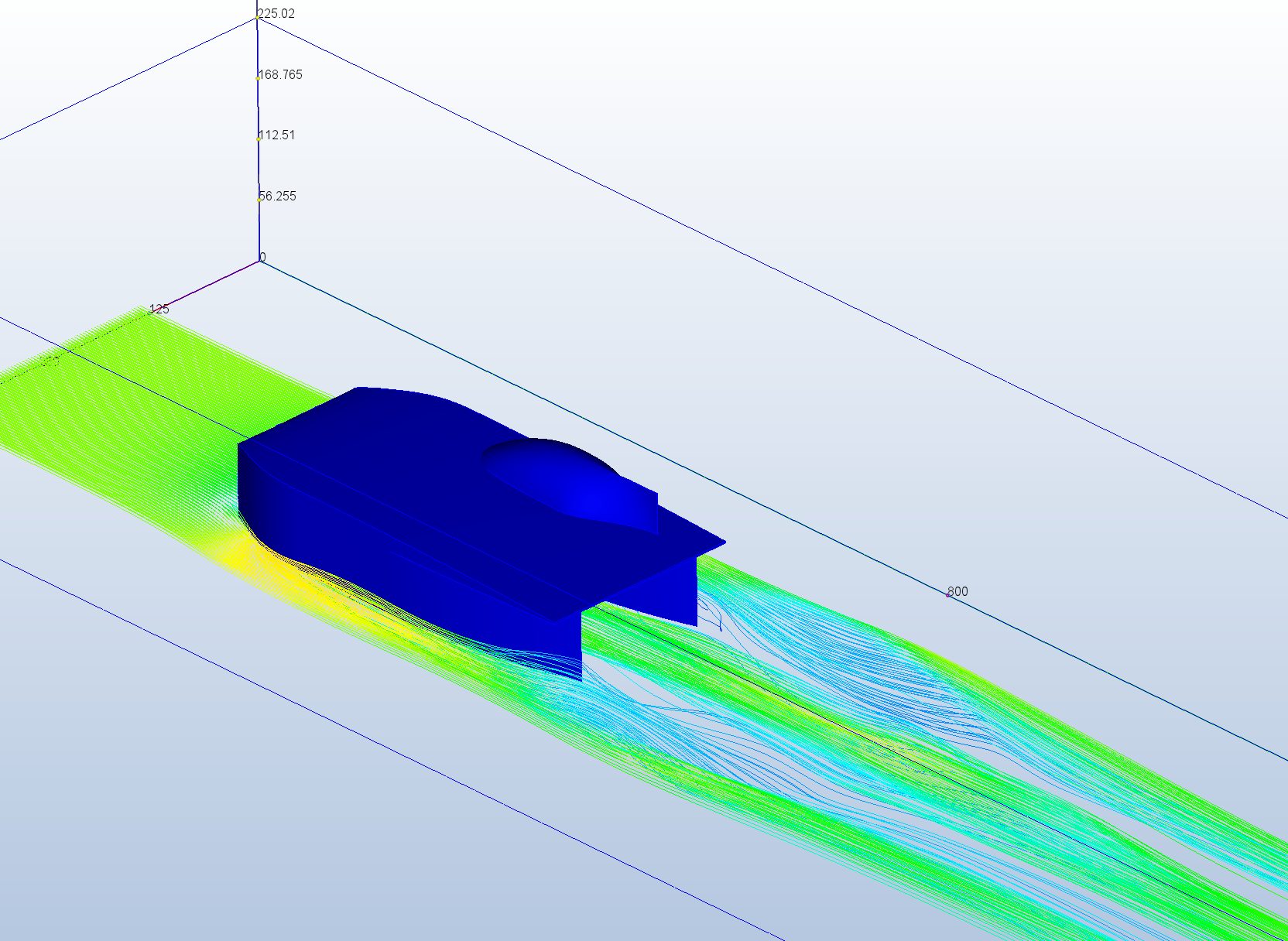
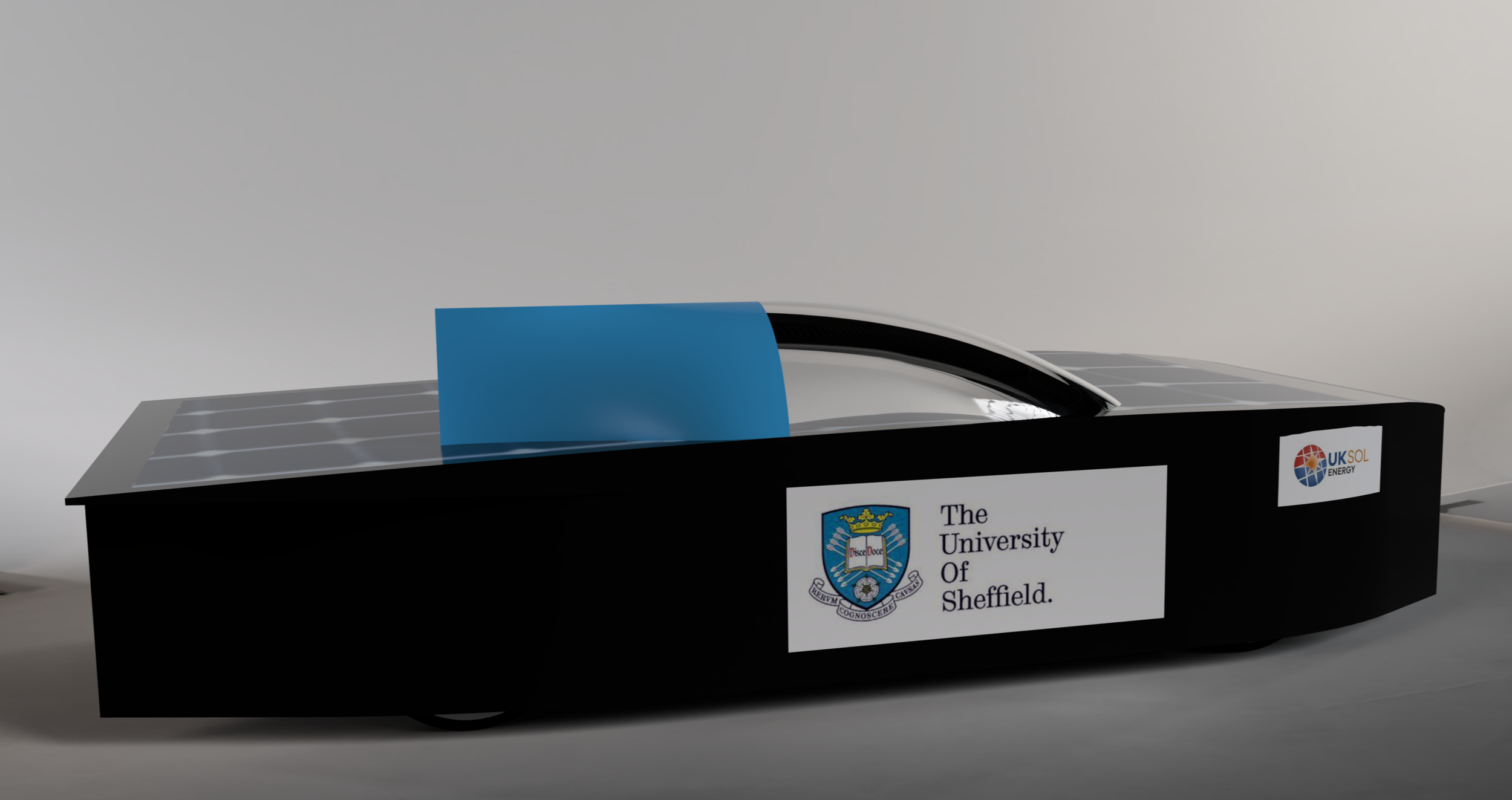

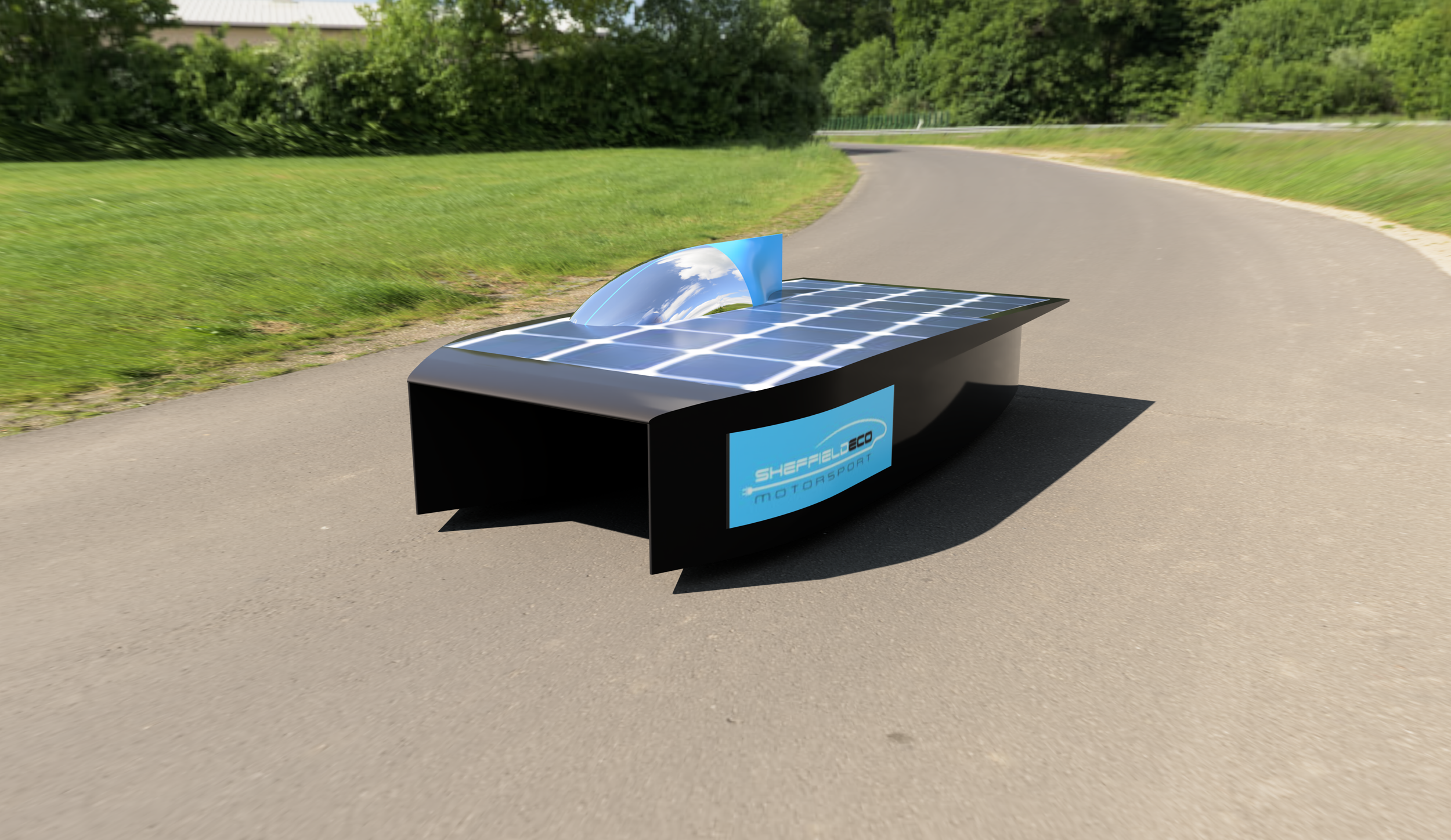

Progress so far:
Body & chassis:
Body
Body have also created countless bodywork iterations in close communication with suspension, control and powertrain to ensure everything fits within the bodywork.
Body have also conducted extensive CFD simulations to inform design changes and verify car performance and characteristics such as Cd for other subteams.
Chassis
By taking the maximum dimensions of the rules and logistics containers, chassis has developed many iterations of steel square tube spaced frame chassis.
Chassis team members have conducted FEA tests to check the design passes the rigorous safety checks mandated by the rules to protect the driver.
Chassis have also worked on designing hard points and minimising weight despite the material choice.
Control & Electronics
Electronics
The focus for electronics with SEM-03 has been the sourcing and choosing of solar panels and associated technology.
With the regulations specfic on where lights need to go electronics have worked on procuring and placing brake, indication and beam lights around the car.
Control
Have implemented an emergency stop button in a safe and aerodynamic place.
Suspension, steering & brakes
Suspension
Suspension have created initial iterations for the front double wishbone suspension and the rear trailing arm suspension.
This involved obtaining and in depth understanding of suspension dynamics and the use of advanced suspension simulation software.
The suspenions is compactly packeged to provide optimal dynamic performance combined with low aerodynamic penalties with co-ordination with body.
Steering
Steering have calaculted the required steering angles for the minimum turning radius and slelcted a steering rack to procure.
Steering have created a CAD model of the proposed steering system so that it can integrate seamlessly into the suspension
Brakes
Brakes have selected brake pads an calipers that provide racing grade stopping power with minimal weight.
Brakes have managed the integration of the hub motors into the rear wheels.
Brakes have selected rims and tyres to provide optimum grip in all-weather conditions.
Powertrain
Powertrain
Powertrain have worked on creating risk assessments to allow the purchase and development of our 2 in hub motors as well as a bespoke battery system. They have made use of battery simulation tools to simulate the performance and size of the battery.
A large part of powertrains work comes in the form of procuring parts from our suppliers so far as included VESCs and in hub wheel motors.
By liasing with companies in the battery industry powertrain could clearly define the coolign required for the powertrain, eliminating unnecessary drag caused by vents and coolign channels.